利用 MicroJect Advanced 工艺,佛瑞亚(Forvia)集团旗下子公司佛吉亚(Faurecia)展示了一种用于发泡注塑成型的新型制造工艺。其目标是实现可持续的制造过程并提高设计自由度和产品质量。通过结合创新的模具涂层和改进后的工艺控制,制成的可见部件显著更轻并具有完美的表面质量,同时还能减少碳足迹。
发泡注塑成型制品常有表面缺陷, 即所谓的泡孔条纹和银纹,因此直到现在发泡部件都无法被用在可见应用中。MicroJect Advanced新型制造工艺能够生产出具有复杂纹理或其他设计表面的完美可见部件(图 1)。此外,凭借仿生设计——来自于大自然的灵感,这些部件的重量明显减轻且仍能保持稳定。与传统解决方案相比,该工艺可以减少一半的碳足迹。该工艺在K 2022 展会上在注塑机制造商ENGEL的展位上进行了展示,他们利用该技术生产了具有不同纹理表面的车门板和车门饰件样品(标题图)。
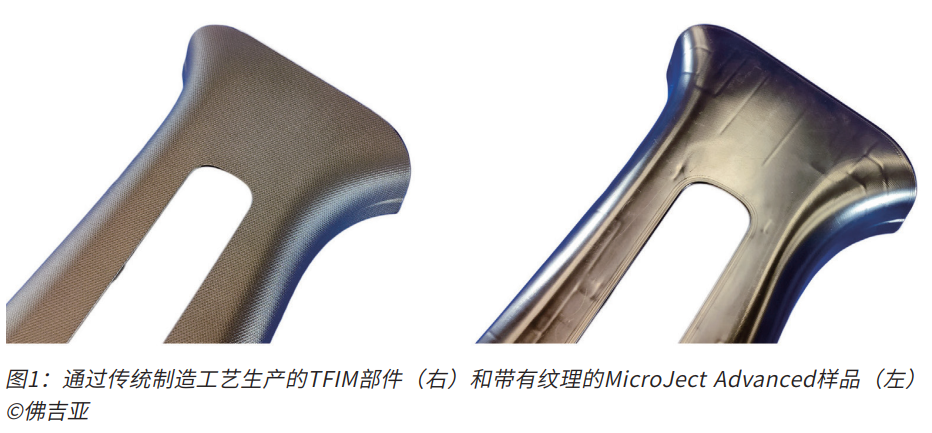
第一步是将惰性气体(CO2或N2)在固定背压条件下溶解在塑料熔体中。在熔体注入模腔的过程中,压力下降导致塑料熔体起泡,就像一瓶汽水的盖子突然被打开了一样。所谓的整体泡沫在注塑模具中产生,形成了具有未发泡表层和发泡芯层的模制品。
如果没有合适的应对措施,部件将具有带泡孔条纹的粗糙表面,导致热塑性发泡注塑成型(TFIM)工艺难以或无法被用在可见应用中。尽管防止或减少条纹产生的解决方案早已出现,其中之一是动态模具温度控制,但它们都无法市场上获得广泛认可。复杂的工艺、更高的设备成本和材料成本、更长的周期时间和高昂的能源成本都限制了的广泛应用。此外,表面质量仍有不足。
被动变温工艺
最新的技术使发泡注塑成型得到了更广泛的应用。创新的模具涂层(制造商:Eschmann Textures International GmbH)可用于生产出具有完美A级表面的TFIM轻质部件。这是一种薄薄的技术陶瓷涂层,也可生成可见部件的纹理。
在注射过程中,陶瓷充当短时的热屏障,使腔壁处的熔体保持塑性状态的时长正好用于积聚足够高的模腔压力来使表面光滑。由于变温(动态)模具冷却具有相似的操作模式,因此尽管没有外部能量供应,我们也可以称之为“被动变温工艺”。尽管进行了隔热操作,但周期时间并未延长。因此,该工艺不仅可以避免泡孔条纹的形成,而且能消除虎纹、光泽差异、压痕和残影乃至明显的熔接痕。
表面纹理通过新型的超短脉冲激光被引入陶瓷涂层。这种激光的脉冲频率比普通商用激光(例如:用于金属表面纹理化的激光)高两个数量级以上。与钢表面相比,陶瓷涂层可以引入更加错综复杂的纹理。因此,该方法为塑料部件的表面带来了全新的设计可能性(图 2),它们未来甚至可被用作高光饰件,无需进行复杂且昂贵的涂装甚至层压加工。
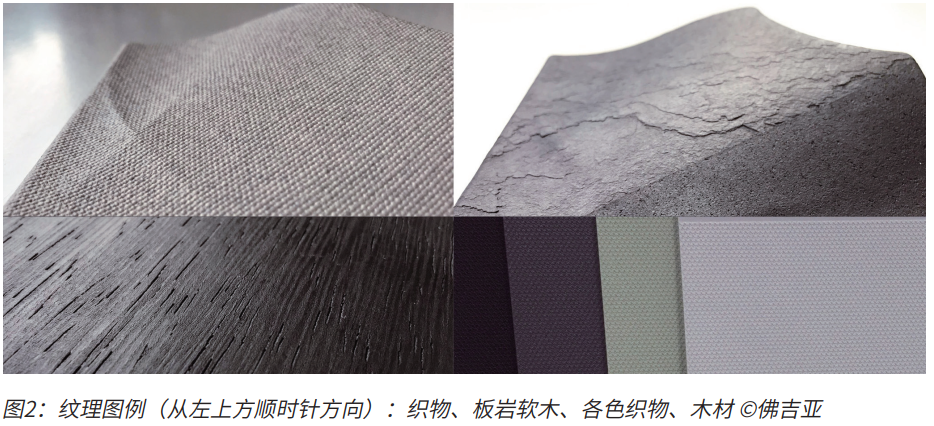
TFIM 整体发泡部件在材料机械性能方面可与夹层结构相媲美,这是因为它们具有出色的重量比弯曲和扭转特性,主要用于飞机、船舶以及风机行业。此外,整体泡沫的截面(外部未发泡内部多孔)与人体骨骼结构相类似。这种三维材料配置在轻量化工程中尤为有用,它并不是唯一来自于大自然的灵感。
仿生学——灵感来自于大自然的轻量化工程
自主研发的CAE仿真程序既可预测整体发泡部件的机械性能(结构仿真),又可预测充气熔体的流动特性(结构仿真)。机械性能不足的部分区域通过加强肋加固,正常情况下,加强肋呈蜂窝状。有肋条的细长结构可被制成与没有肋条的厚实材料一样坚硬,即使材料用量较少。未来,佛吉亚生产的TFIM部件将由轻薄的表层和背部复杂的加强网络组成,就像睡莲植物一样,即使有婴儿坐在上面也不会下沉。
为了避免出现凹痕,肋条和B侧功能部件(螺钉和焊接堵头、夹片和固定器)通常垂直连接到部件背面。但这对力的传递特别不利,因为肋基处的直角排列导致此处应力增加,可能导致肋条失效(缺口效应)。为了尽量减少缺口效应,另一个来自大自然的例子被用到了。在这一点上,他们通过技术手段复制了一棵树的结构。树干所遵循的几何原理能够显著降低缺口效应。因此,所有B侧功能部件都变得更加稳固并且可以传递更大的力。这种功能部件设计并不适用于传统的注塑成型,它只能借助Microject Advanced显著更大的设计自由度来实现。
溶解后的发泡剂显著改善了熔体的流动性(塑化作用),并且非局部发泡压力还使其能够使用更厚的肋条而不会出现凹痕。因此,两者都可以使可见部件比之前更薄。大多数情况下,在更改设计时考虑到发泡通常可以节省10-20%的材料。即使是薄壁部件,发泡工艺本身也可以帮助其进一步减少5-7%的重量。
可持续性和轻量化
除了在K 2022展会上通过物理发泡(MuCell 工艺)生产具有不同纹理表面的样品,佛吉亚还展示了一个车门饰件样品(图3),它比未发泡的同类产品轻23%。其中,17%来自于上述设计的更改,6%来自于发泡本身。由于模腔压力显著降低,部件仅需10,000kN的锁模力即可生产,而未发泡产品至少需要18,000kN的锁模力。
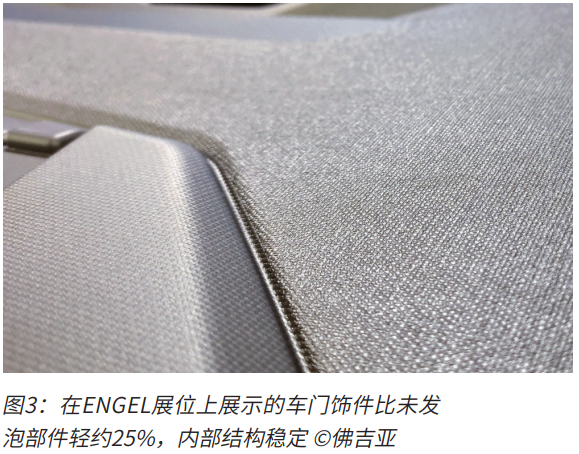
与未发泡的注塑件相比,发泡车门饰件所需的能量明显更少,因为它所需的锁模力较低并且本身的材料消耗较少。佛吉亚开展的全球变暖潜能值(GWP)的生命周期评估(LCA)表明,该生产工艺的碳足迹减少了一半。获取和制造所需原材料排放的二氧化碳减少了 23%。
为了使产品更具可持续性,部件注入了新开发的高回收率聚丙烯。该化合物由佛吉亚可持续材料部(SMD)的专家专为新技术而开发。除了良好的发泡性外,材料开发还侧重于哑光的防刮擦表面。开发人员认为,织物表面柔软的触感非常重要,即使纹理不同,柔软的触感也能使部件表面令人感觉愉悦。如果将创新的纹理与聚合物定制的着色剂相结合,则能进一步突出纹理特征,并带来更真实的视觉体验。该新技术已在数月之前成功完成验证。






